A New Approach to New Knees
A Mount Sinai orthopedic surgeon is using 3D printing, AI, and advanced robotics to revolutionize joint replacements.
Knee replacements have been done essentially the same way since 1968.
For patients suffering from degenerative osteoarthritis, total knee arthroplasty can dramatically reduce pain and restore mobility. But for every nine successful procedures, one fails. The patient then requires a complex follow-up surgery to address issues such as wear, loosening, instability, and infection.
Most patients get off-the-shelf implants, and the majority of implants are attached to bone with cement, which can break down after a couple of decades.
But an innovative new approach is poised to reinvent traditional replacement surgery procedures.
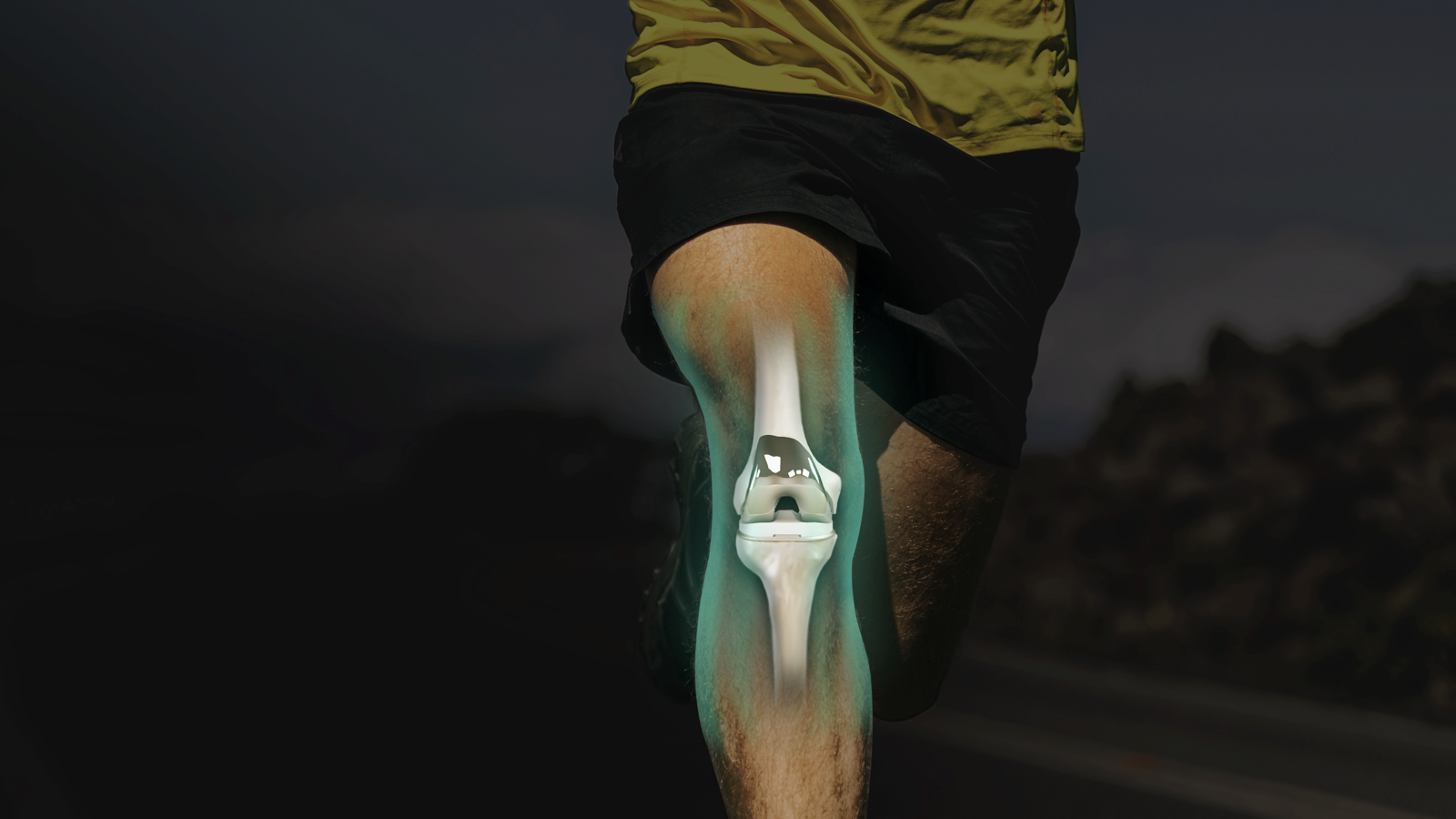
The overall joint replacement market is currently valued at $19.6 billion and is ripe for disruption.
Monogram scans a patient's knee structure, uses this data and AI to design and print a customized implant, and inserts the implant with the aid of a surgical robot for better accuracy.
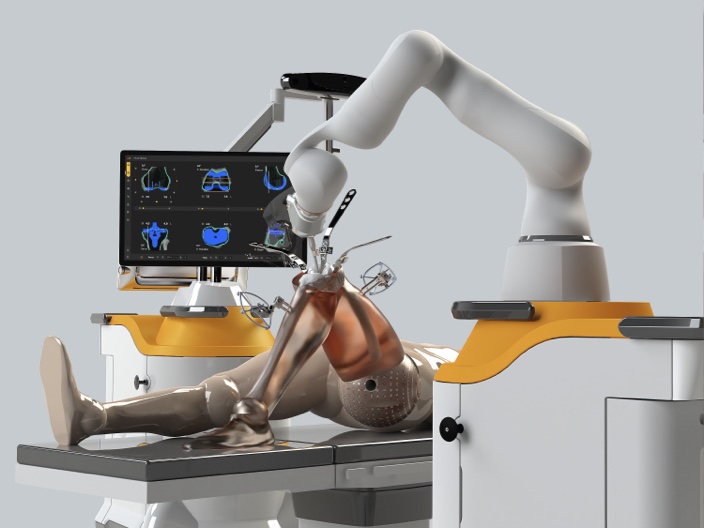
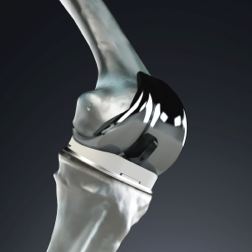
The Innovator
Dr. Douglas Unis is a board-certified attending orthopedic surgeon for the Mount Sinai Health System and Chief of Quality Improvement for Mount Sinai West. Building upon an interest in robotics that began at Case Western Reserve University School of Medicine, he founded Monogram Orthopedics with the goal of using robotics, 3D printing, and digital image analysis algorithms to enable safer, more efficient, longer-lasting joint replacements.
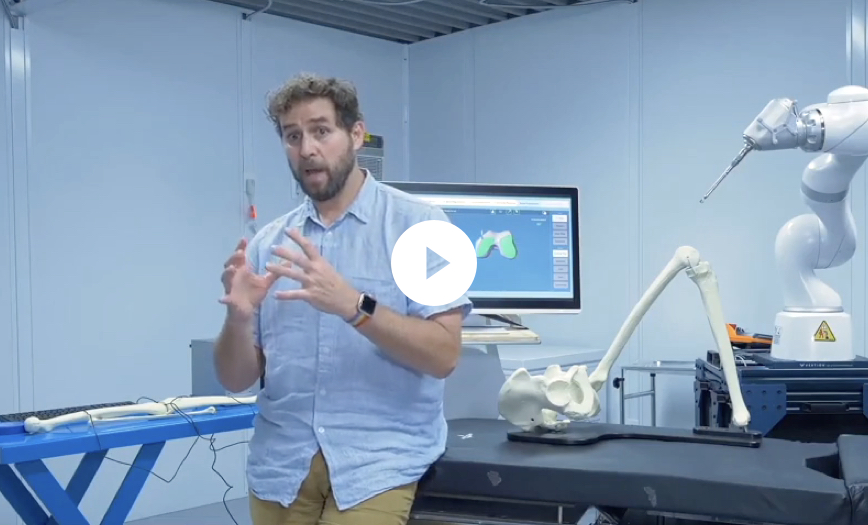
In 2013, a medical technology company asked Dr. Unis to consult on a new orthopedic surgery system that used a computer-guided robot to help surgeons more accurately insert implants. Dr. Unis was impressed by the potential the system offered. But he was underwhelmed by the actual execution. Early robotic surgery systems, he says, were "trying to make an Atari play an Xbox game."
He knew that a better joint-replacement solution would result in improved outcomes for patients. It could be big business, too. The overall joint replacement market is currently valued at $19.6 billion and is expected to increase 250 percent by 2030.
By 2027, approximately 50% of all knee procedures will be robotic, up from 11% in 2019.
It seemed like a daunting challenge. But Dr. Unis and his team of experts in surgical robotics and implant design believed the monolithic scale of the competitors made them susceptible to a nimble newcomer. "They're not built to innovate," he says. "They're built to have big distribution networks and sales forces."
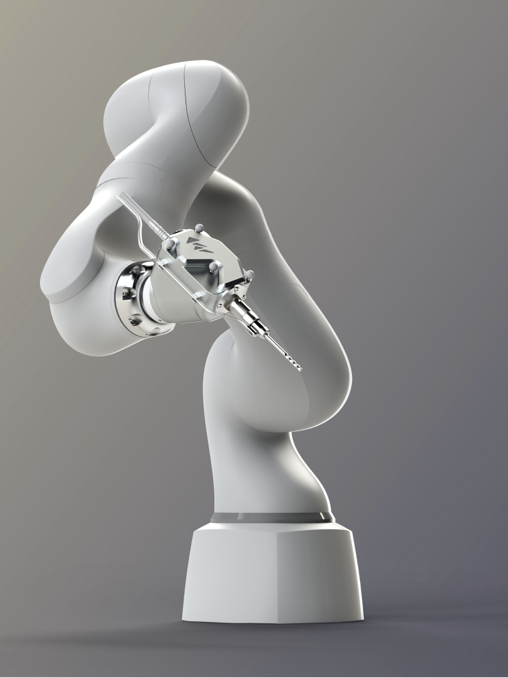
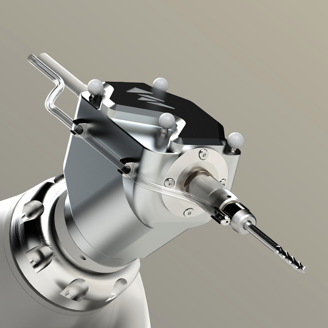
Robotic Knee Replacement
Monogram began with a German industrial robot designed for manufacturing but adaptable to surgery. They mounted cutting tools on its flexible 1.3-meter arm. They added a suite of cameras to give the surgeon a clear line of sight. And they gave the robot sensors to monitor force and help the surgeon avoid healthy tissue.
Most important, they created a platform in which the robot uses 3D imagery of the patient's knee anatomy to help the surgeon move efficiently, make precise bone cuts, and navigate small spaces.
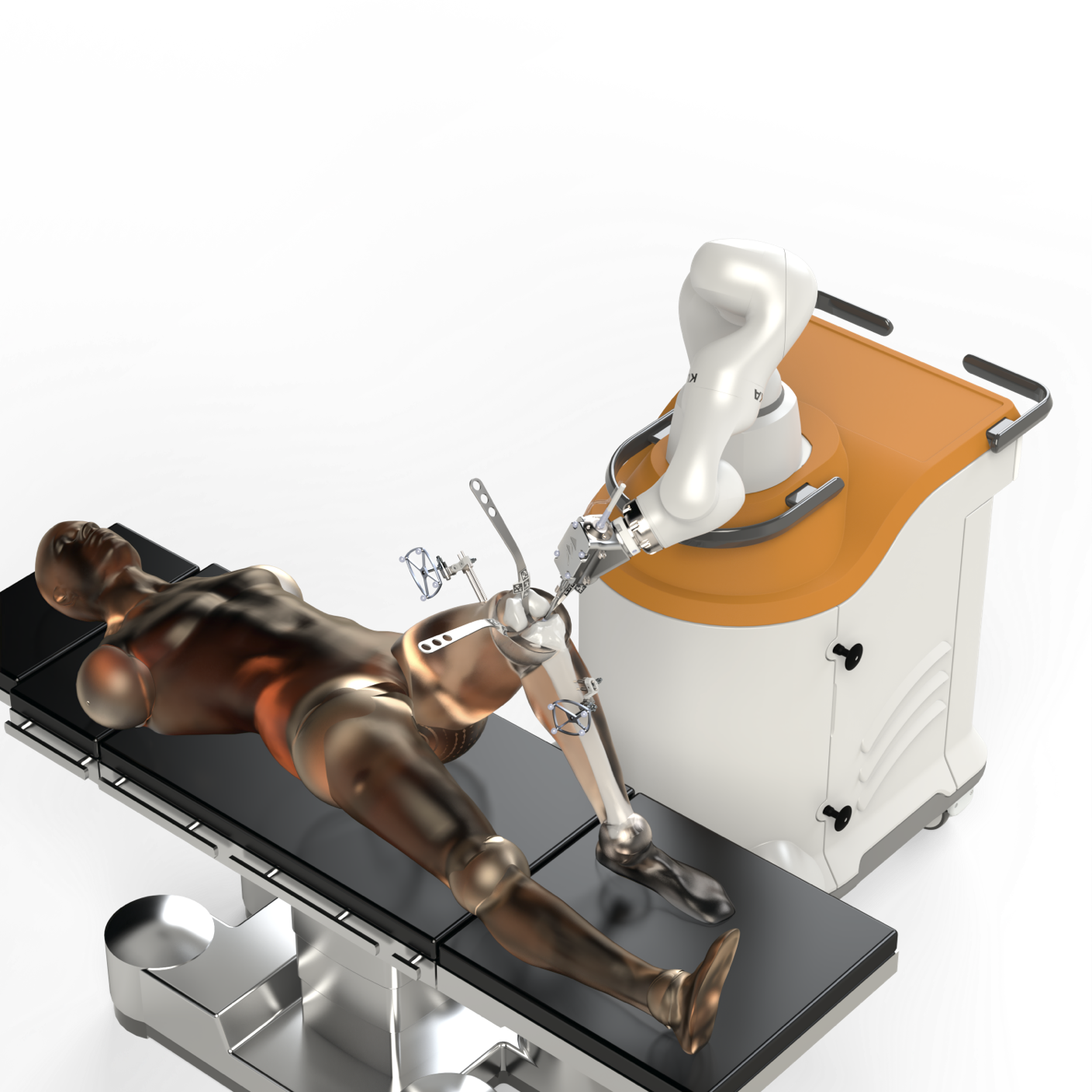
Monogram Orthopedics had a singularly ambitious goal: to disrupt the emerging orthopedic robotics oligopoly dominated by four companies that control 90 percent of the market.
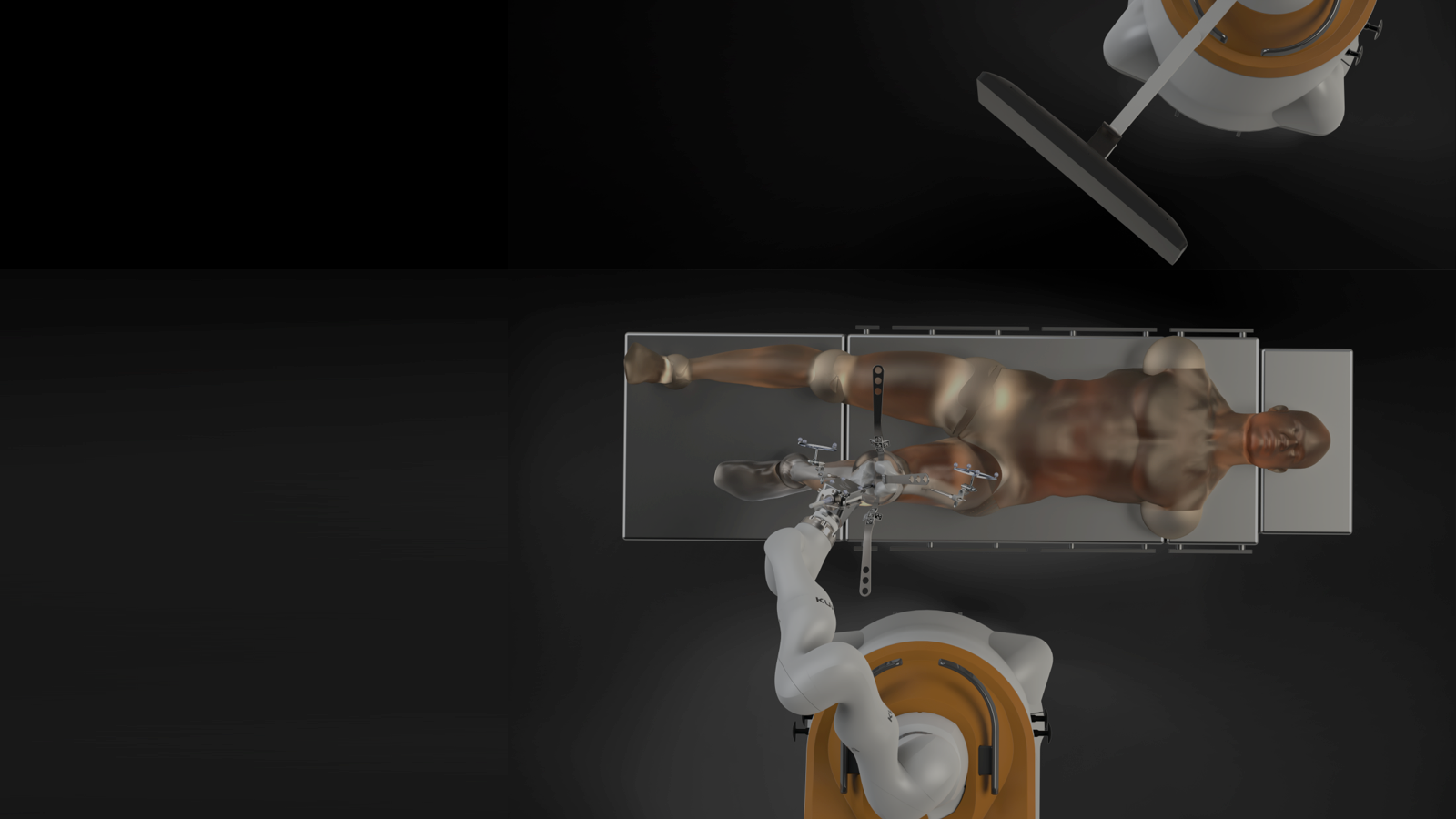
The robotic arm uses 3D imaging data to help the surgeon prepare the bone, introduce the implant, and check for any problems.
The Bee's Knees
The surgical approach wasn't the only problem Dr. Unis saw with current robotic solutions. "I kept thinking, why are you going through all this effort to put in a generic implant?" Getting an implant today is a little like walking into a clothing store where there's just one style of shirt in a limited range of standard sizes. Dr. Unis believed that by customizing implants to the unique anatomy of each patient, they would fit better, last longer, and give better results. So Dr. Unis and the Monogram team developed an artificial intelligence software that designs customized implants based on computed tomography scans of a patient's anatomy.
To produce the implants, Monogram employs a refrigerator-sized 3D printer that can create 30 implants a day from medical-grade powdered titanium alloy.
These customized implants are designed to be implanted without cement. The surfaces that contact bone are porous—"sort of like an English muffin," Dr. Unis says—allowing bone to grow into and around them. This creates a much stronger bond than cement.
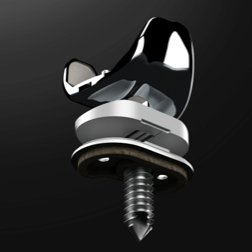
Developing this technology required funding, and Monogram received its seed funding through Mount Sinai's i3 Accelerator program. But it soon needed more. In medtech, the Catch-22 is that you need more money to raise more money.
To have something that's going to be of interest to a venture capitalist, you need millions of dollars and a big team of engineers.
Monogram bypassed banks and venture capitalists and launched its own crowdfunding campaign on StartEngine, a sort of Kickstarter for startups and private businesses. This let it connect directly with individual investors. The campaign's success stunned even the Monogram team. By the time the offering ended on February 19, 2022, Monogram had raised $23,793,182 from 14,082 investors.
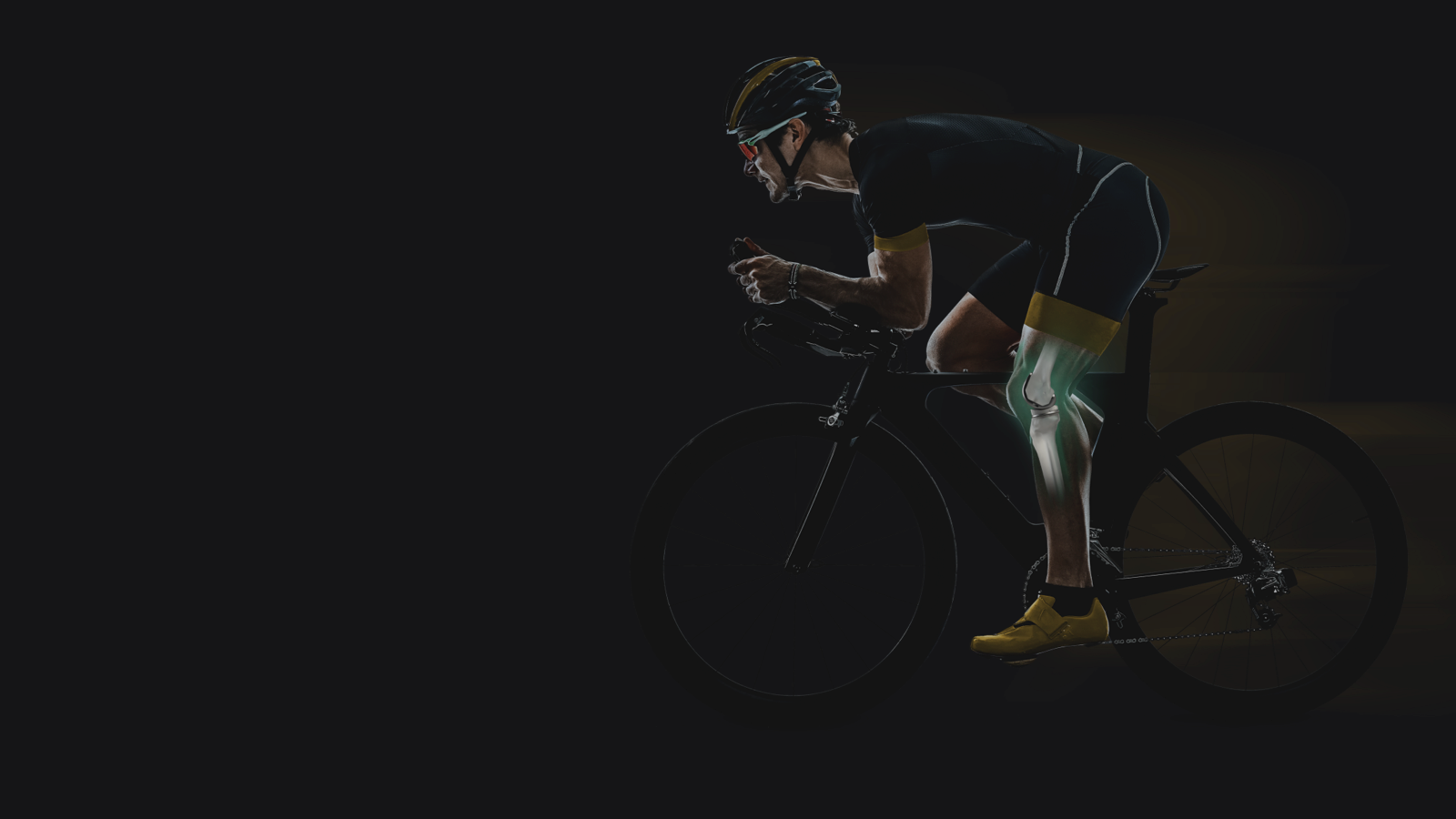
At one point, Elon Musk was making two-seater electric cars for movie stars, and everyone was laughing at him. But now you watch the Super Bowl, and half the ads are for electric vehicles. We'll all be driving them in 10 years. It's the same for orthopedics. We'd like to be the people moving the ball forward.
The Path Forward
Thirty years ago, Dr. Unis says, typical candidates for knee-replacement surgery were 70 years of age or older, and often they simply needed to regain their mobility. Today the patients are younger and more demanding. "I have triathletes," Dr. Unis says, "and people who want to get back to rock climbing."
Monogram is moving quickly to give these patients a better option. To date, the company has filed for 14 patents to protect its technology, won a grant from the National Science Foundation to support its work, and recently built a cadaver lab that resembles an operating room. Here, the team can test and demonstrate its technology as it works toward approval from the U.S. Food and Drug Administration and ultimately bringing the system to market.
Mount Sinai continues to support the work. The health system has an equity stake in Monogram, and in turn Monogram licenses patents from Mount Sinai. Dr. Unis continues to teach and do clinical rounds at Mount Sinai, and credits the health system for its ongoing support of Monogram. "I wouldn't have gotten this off the ground anywhere but here," he says. "I had institutional support."
This relationship is about more than building a business. It's a demonstration of how Mount Sinai and its partners are developing and scaling solutions that continue to advance medicine and change lives.
Better by BioDesign
Inside the incubator that brings innovative ideas to life in 3D
While launching Monogram, Dr. Unis worked closely with the team at Mount Sinai BioDesign, a venture at Mount Sinai that works with physicians, inventors, and others to translate concepts into viable products. Ideas that may start with simple sketches are developed, prototyped, and then turned into real-world products and businesses. Mount Sinai BioDesign also works with doctors; 3D printing of anatomical scans such as this skull can help surgeons plan procedures.
Drag to rotate